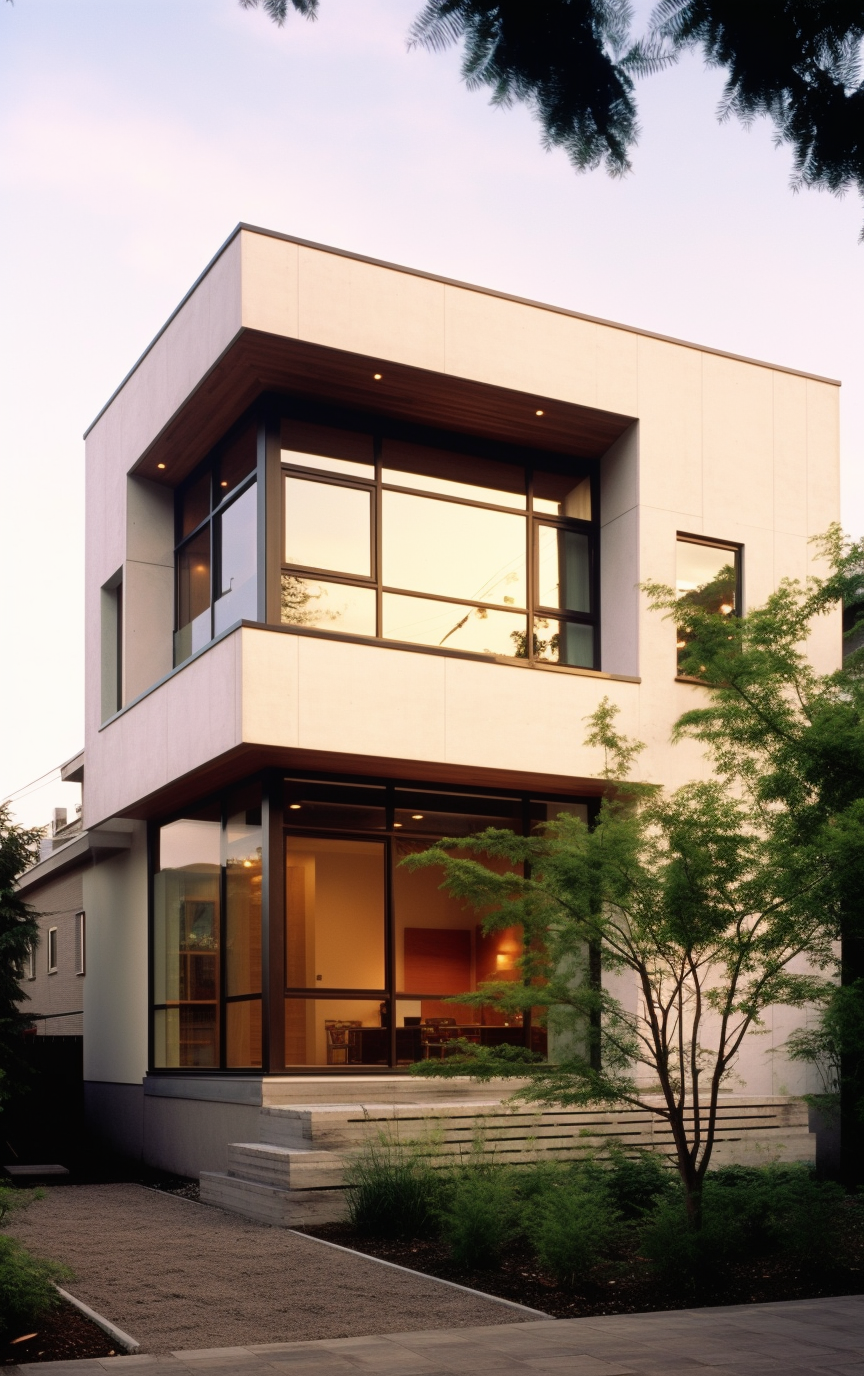
Implementing Quality Assurance Processes in Construction Projects
QA in construction plays a major role in making sure every construction project meets the right quality standards. It’s not just about checking for mistakes—it’s about following a proactive approach to avoid them in the first place. Quality assurance in construction focuses on setting up systems to ensure that materials, methods, and outcomes meet the project’s specification and quality requirements.
Over the years, quality assurance (QA) and quality control (QC) have both become more advanced in the construction industry. Today, builders use quality management systems, quality management software, and even tools like BIM to improve accuracy and reduce rework. Construction quality assurance helps teams ensure compliance, deliver a solid final product, and increase customer satisfaction. It also makes it easier to catch potential issues early and rectify them before they affect the quality of work.
In this guide, we’ll explore how to implement strong quality assurance processes in any construction process. You’ll learn how QA and QC work together, how to perform proper inspection, and how to build a systematic management system that meets all project requirements. We’ll also look at how to handle compliance, manage supplier quality, and make sure every stakeholder is aligned. A strong QA plan helps your team adhere to plans, reduce errors, and deliver outstanding workmanship from start to finish.
Understanding Quality Assurance in Construction
Quality Assurance (QA) in construction refers to the systematic processes and procedures used to ensure that a project meets defined standards and specifications throughout its lifecycle. Unlike Quality Control (QC), which focuses on defect identification and correction, QA emphasizes preventing issues through planned and systematic activities.
Planning for Quality Assurance
Planning for effective quality management is crucial in the construction process, setting the foundation for meeting stringent standards and achieving project excellence. By embedding recognized best practices early on, projects can significantly reduce the risk of costly reworks and delays, ensuring a smoother path to completion.
- Define Objectives: Establish clear, achievable quality goals that are in line with client needs and regulatory requirements.
- Establish Procedures: Implement detailed, standardized methods to consistently meet or exceed quality benchmarks.
- Training Programs: Equip team members with the necessary skills and knowledge through targeted training initiatives.
- Regular Audits and Inspections: Schedule systematic reviews to ensure ongoing compliance with the quality plan.
- Documentation Management: Maintain thorough records of all quality-related activities for accountability and continuous improvement.
- Plan Review and Updates: Continually assess the plan's effectiveness, incorporating feedback to refine quality measures.
Incorporating these elements into the early stages of project planning underscores the importance of a proactive approach to quality assurance.
Implementing QA Processes
Integrating QA processes throughout construction phases ensures projects meet standards from groundwork to completion. Experts advocate for embedding QA measures early, with case studies demonstrating reduced errors and rework. Technologies like Building Information Modeling (BIM) have revolutionized QA, allowing for precise planning and error detection before construction begins. Projects utilizing BIM for QA have reported significant improvements in accuracy, efficiency, and overall project timelines, underscoring the technology's impact on modern construction practices.
Key Elements of a Successful QA Process
Ensuring a construction project's success involves several critical components, each contributing to the overall quality and efficiency. Drawing insights from construction experts and supported by data-driven studies, the following points highlight essential aspects of an effective quality management system.
- Comprehensive Documentation: Essential for tracking progress and identifying areas for improvement, detailed records support accountability and facilitate continuous improvement processes.
- Regular Inspections and Audits: Scheduled assessments at various project stages are crucial for ensuring adherence to standards, significantly reducing the likelihood of defects and minimizing rework costs.
- Targeted Training Programs: Training staff and subcontractors on specific practices and standards aligns all team members with the project’s quality objectives, directly impacting the outcome’s quality.
- Subcontractor and Supplier Management: Rigorous vetting ensures that all materials and workmanship align with the project's requirements. Effective management is linked to enhanced project quality and adherence to timelines.
- Continuous Feedback and Improvement: A system for collecting and implementing feedback from audits and team inputs allows for the ongoing refinement of processes, making them more effective over time.
- Leveraging Technology: Adoption of technologies like BIM and quality management software improves the precision of quality processes. Projects utilizing these tools report significant enhancements in meeting standards and reducing errors.
Focusing on these components cultivates a quality-centric culture within the project team. Prioritizing accurate documentation, thorough inspections, comprehensive training, and the strategic management of subcontractors and suppliers ensures high quality levels.
Quality Assurance Tools and Techniques
Embracing modern tools and technologies is essential for enhancing project outcomes in construction. Below is a list of key tools that have transformed QA processes, contributing to their effectiveness and efficiency:
- Building Information Modeling (BIM)
- QA/QC Software Platforms
- Digital Checklists and Mobile Apps
- Drones for Aerial Site Inspections
- Wearable Technology for Safety Monitoring
- 3D Scanning and Photogrammetry
These tools have been instrumental in elevating the QA process, enabling teams to achieve higher accuracy and consistency across construction projects.
The Benefits of Effective QA Processes
Effective QA processes bring significant benefits to construction projects, especially:
- Cost Savings: By minimizing rework and waste, effective QA processes can reduce overall project costs by up to 20%, according to a study by the Construction Management Association of America.
- Efficiency Gains: Projects implementing advanced QA processes report a 15% improvement in project completion times, showcasing the efficiency benefits of a well-structured QA system.
- Improved Client Satisfaction: With higher quality outcomes, client satisfaction rates increase, with surveys indicating a 30% rise in client approval for projects adhering to stringent QA standards.
- Competitive Advantage: Firms that consistently apply rigorous QA processes tend to win more bids, as quality assurance becomes a key differentiator in the market.
- Enhanced Reputation: Positive testimonials from satisfied clients and a portfolio of successful projects contribute to a stronger reputation, making it easier to attract new business and top talent.
These benefits highlight the value of integrating robust QA processes into construction projects, not just for immediate project success but also for long-term business growth and reputation.
Conclusion
Implementing Quality Assurance (QA) processes in construction projects is indispensable, ensuring projects meet the highest standards of quality, efficiency, and safety. This critical approach requires ongoing education and the adaptation of new standards and technologies, fostering a culture of continuous improvement and excellence within the construction industry.
For those looking to elevate their construction projects with top-tier QA processes, MR Home Remodeling offers expert services tailored to your needs. Embrace the benefits of rigorous quality assurance with MR Home Remodeling and set your projects apart with unmatched quality and client satisfaction.